Advanced LenSystem Saving 50% in cost.
The ODC lens system creates a finished Rx directly from liquid monomer, eliminating the need to cast a semi-finished blank that is later surfaced to the final prescription.
The ODC lens system creates a finished Rx directly from liquid monomer, eliminating the need to cast a semi-finished blank that is later surfaced to the final prescription. This eliminates the costs and slow delivery challenges associated with casting, shipping, and managing inventory for thick semi-finished lens blanks. This process also reduces the variables of surfacing and ensures that consistent, high quality lenses can be produced at a much lower cost. The cast-to-Rx process is computerized and straightforward for the practitioner's existing staff to master. All lens types can be cast and dispensed in clear or Photochromic materials in under an hour, while saving as much as 50% or more on lens costs.
NanoCLEAR AR lenses can be produced in less than one hour, while other offices wait 3 to 14 days for AR lenses from a lab. With ODC increased service increases patient flow, lab wholesale costs are greatly reduced and more patients choose premium lens products. These three factors typically improve practice net income by up to 50% or more.
The simplest form of ophthalmic lenses is referred to as single vision lenses.
The term Premium Lenses refers to: Lenses that have more than one focal distance (multifocals), progressives, digital lenses, freeform designs, progressive addition lenses, computer lenses, aspheric, atorics, melanin, and photochromic lenses.
The traditional lens distribution channel is multi-stepped which makes the cost of premium products much higher than single vision. ODC technology compresses and eliminates thereby capturing significant value in the lens distribution channel.
ODC was the first lens company to earn a prestigious double certification from COLTS (Certified Optical Lens Testing) Laboratories for product performance and prescription quality. These certifications were awarded after our system and lenses passed an exhaustive series of tests designed to verify the quality and consistency of our products. All of our lens casting systems include self diagnostics and continuous monitoring of critical system parameters to ensure premium quality lenses are produced every time.
SRI International, founded as Stanford Research Institute is one of the world's most prestigious research facilities. They are based in Menlo Park, California and employ more than 1700 PhDs. Their mission is discovery and application of science and technology for knowledge, commerce prosperity and peace.
The Advanced Automation Center, Sensory Science Laboratory, Applied Electromagnetic and Optics Laboratory, and the Polymer Chemistry and Technology Group all studied the feasibility of the ODC technology. They conducted two technology reviews and concluded that: They were impressed with the ease and swiftness by which with only minimal training, lenses can be produced. The ability to deliver premium lenses within an hour gives the producer the marketable advantage they need to plan and promote their business. The technology allows market share increases to be driven without the expense of inventory. These benefits seem tangible and achievable. SRI ranks these benefits as HIGH. This method should become the standard for in-store delivery. This technology has the ability to revolutionize the way glasses are delivered to patients.
Anti-Reflection and Nanomaterials
- An AR coating is achieved by depositing nano-composite films of alternating refractive indexes
- By engineering the refractive indexes and thicknesses of these films, visible reflections are reduced and transmittance is improved
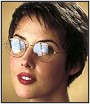

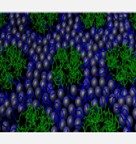
nanoCLEAR AR:
Nanotechnology refers to the engineering of structures than are less than 1OOnm, (a piece of paper is approximately 150,000nm thick). Using UV-curing technology and nanoparticles we were able to develop thin films that cancel the reflections from a lens surface . This allows the production of AR lenses at an affordable cost.
This equipment is designed to be used with the Q2100R. The entire process is microprocessor controlled. The operator merely places the molds into the front of the system and presses the start button. The robotic arm shuttles between cleaning, coating and curing inside the system. HEPA filters keep the environment inside the chamber clean. Once the process is started the operator can attend to other duties. The small tabletop design allows easy placement in any office. The clean, quiet device is WIFI enabled for quick seamless updates and system diagnostics by real time, on-line diagnostics. Competing technologies cost 10 to a 100 times more than the nanoCLEAR AR Our scientists use cutting-edge nanoparticle technology to engineer the refractive index of each AR layer. By incorporating nanoparticles into the polymer matrix allows for the engineering of the refractive indices ranging from 1.46 all the way to a refractive index of 2.70. This allows ODC lenses to be born anti-reflective, anti-scratch and anti-UV. Not coated after the lens is produced which is today the norm in the industry. Nanoparticles allow us to improve mechanical performance and engineer the refractive index over a broad range. Another advantage of using a polymer based coating on a plastic substrate is the strain domains are similar, so there is less chance of cracking or delaminating the films from the substrate. The inherent dissimilarities between conventional vacuum deposited ceramic coatings on top of a plastic lens cause a myriad of problems. To avoid these pitfalls, ODC developed an anti-reflective technology which is plastic in nature. The normal industry cyclic humidity testing proves this type of coating performs better in real world situations . COLTS Laboratories RLS (Real Life Simulation) testing verifies these claims.
Another issue that plagues vacuum deposited anti-reflective coatings is the clean ability of the lens. A vacuum deposited AR coating leaves a columnar structure that traps oils and dirt and is difficult to clean. The patient becomes aware of this when he sees smudges and smears on the lens surface. In response to this problem the industry developed hydrophobic coatings to fill the valleys and produce a smooth surface. The nanoCLEAR product is inherently smooth, hence cleaning remains easier over the life of the lens. Cleanability and durability are the two major failure modes of conventional vacuum coating. The ODC solution to these issues dramatically improves patient satisfaction.
NASA Award:
NASA (National Aeronautics & Space Administration) US has been interested in nano based products for several years. They realize the coatings incorporating nanoparticles that are as thin as 100 nm can dramatically improve the mechanical performance of an underlying substrate. The same technology that can be used for visible light can be effective with other electromagnetic waves.
Coatings can be designed to target specific wavelengths. These coatings will have advantages in flexibility, durability, cost, ease of use and curing speeds. For these breakthroughs, this technology was awarded the NASA Nano Award !
- Nano-scale additives must be used to avoid transmittance losses and scattering that occur with larger particles
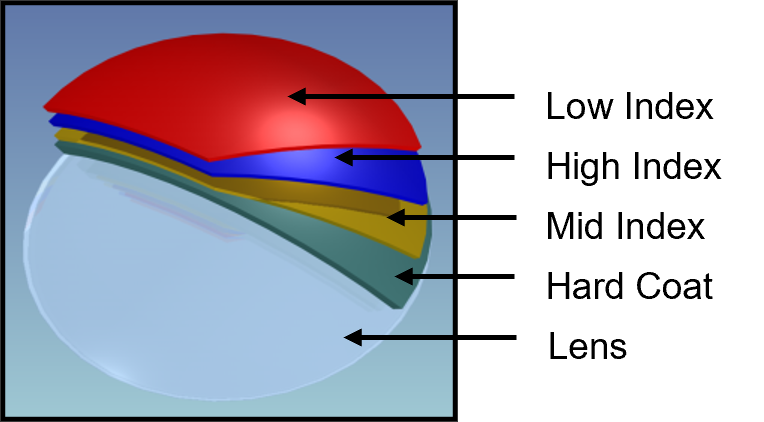
Nano-composite coating benefits:
- Increased ability to engineer refractive index
- Increased mechanical performance due to the hardness of the particles
The ODC lens system creates a finished Rx directly from liquid monomer, eliminating the need to cast a semi-finished blank that is later surfaced to the final prescription.
All lens types can be cast and dispensed in clear or Photochromic materials in under an hour, while saving as much as 50% or more on lens costs.